

Mission
September 2017 – May 2018
ME 415: Pre-CAPSTONE course, introduced my class to designing and building a brick producing machine for a village in Uganda. The class was split into teams of five to design and produce the subsystems. My team was assigned the extrusion system that pressurizes the mixed clay and pushes it through the nozzle.
The extruder system was difficult to start. None of our team had background knowledge in auger screws or extrusion prior to this project. To prepare for this project, I began looking up existing machines and watching many YouTube videos on them. I also knew we would need experience in flow analysis so I began looking through SolidWorks resources and borrowed a training book from our instructor Dave Torick.
Design & Analysis




To start, our team looked at the required mass flow rate needed to achieve 20,000 bricks per day. Once we calculated the mass flow rate we chose an arbitrary pipe diameter to run a flow analysis to see what magnitude of power and RPM it required. We then varied the diameter to begin optimizing the system.
The second concept design included the hopper to connect the extruder to the mixing subsystem. Adding the hopper and gravity added some complexity to the flow analysis.
Because of my determination to learn flow analysis, I took responsibility to lead the analysis. This particular analysis took several steps and trials because clay is non-newtonian. To simplify the analysis, I began with replacing the fluid with water and using the concept 1 model. After completing this simple test analysis, I used global variables to optimize the pitch and diameter of the auger screw. Next, I added the hopper and gravity back in. I verified that the auger screw was still optimal within this test and then replaced the water with a more viscous material that was built into SolidWorks. Because the mud and water mixture could vary at the Ugandan site, I had to estimate and test a couple variations of material properties within the simulation. Other problems included meshing the auger screw properly and changing the controlled volume to speed up calculation times, some of the studies took many hours.
Once the analysis was compete, we designed a half scale version of our model to prototype.
Prototype
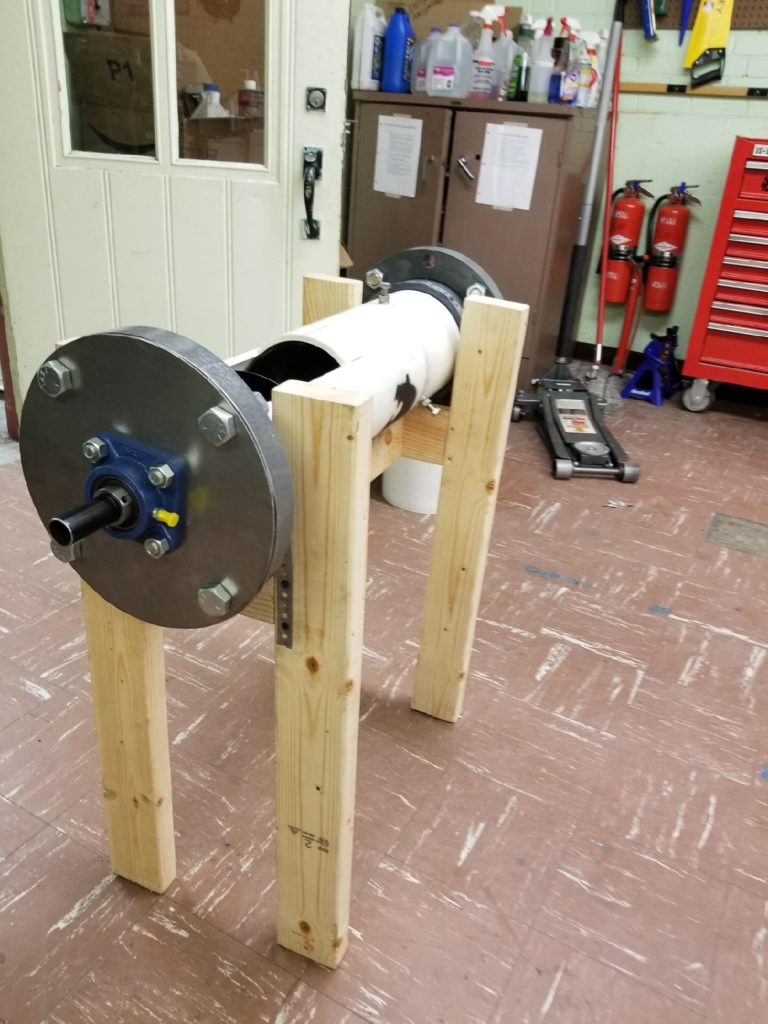


One of my team members took responsibility in building the prototype. He did an excellent job.
Testing
Our prototype did not preform as well as we expected. However, the mixing team never completed their prototype which directly affected our subsystem because we had to mix the mud and clay in at the hopper, leading to efficiency loss. Other possibilities could be that the analysis didn’t represent the clay accurately or that we had mechanical power transfer loss within our system.
Conclusion
After testing was completed, I was one of two team members to produce the drawing package for the final full scale design. Unfortunately, I cannot find the drawing package, hopefully it will be uploaded soon.
Our team preformed the best out of the class even with having the most challenging subsystem. I grant this to our team communicating effectively with one another and taking advantage of each other’s strengths.
Because the system wasn’t perfect by the end of the semester, the class project was picked up by the Humanities Engineering at WSU Club (HEWS). I joined the club to continue help develop this further. Within the club, I lead the extrusion team to make it easier to manufacture in Uganda. The first concern was making the auger screw. We knew they had limited maching tools so we changed the design to be a 4 inch pipe that they would shape rebar into fins around it and weld it all together. This would end up saving the client a lot of money, however, we never got to the point to testing this design. Additionally, I helped with assembling and testing the new mixing team assembly.